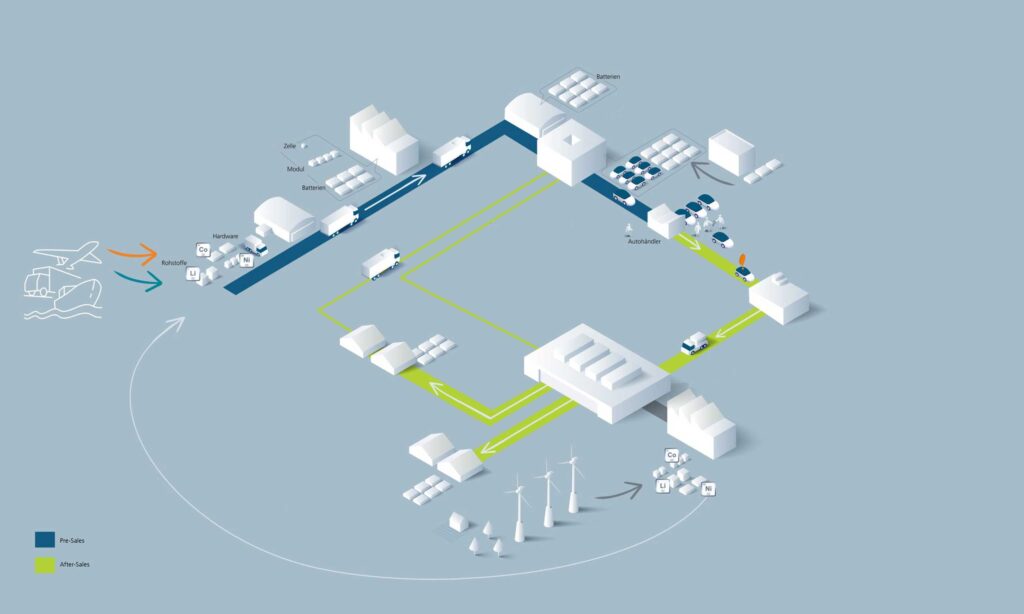
Der Bestand der batterieelektrischen Pkw weltweit ist laut Statista von 0,4 auf 17,4 Millionen in nicht einmal einem Jahrzehnt gestiegen. Allein in Deutschland soll die Zahl bis zum Ende dieses Jahrzehnts nach dem Willen der Bundesregierung auf 15 Millionen steigen. Der jüngste Beschluss der Europäischen Union – Stichwort »Verbrenner-Aus« – wird dieser Entwicklung noch einmal Schub geben. Mit der Zahl der Fahrzeuge steigt naturgemäß auch die Zahl der Fahrzeugbatterien. Sie machen den größten Wertanteil am Pkw aus.
Auf Wachstumskurs
Bestand der batterieelektrischen Pkw (BEV & PHEV) weltweit:
2013: 0,43 Mio. | 2015: 1,4 Mio. | 2017: 3,4 Mio. | 2019: 7,8 Mio. | 2021: 17,4 Mio.
Quelle: statista
»Allerdings ist die Batterie heute – (nicht nur) aus logistischer Sicht – noch eine Black Box, die ein großes technisches und wirtschaftliches Risiko birgt«, sagt Max Plotnikov vom Innovationslabor für Batterie-Logistik in der E-Mobilität, wissenschaftlicher Mitarbeiter des Fraunhofer IML, dem Konsortialführer des Projekts. »Batteriehersteller oder Automobilhersteller, die darauf bedacht sind, funktionsfähige und sichere Produkte effizient am Markt zu platzieren, sehen grundsätzlich ein eher geringes Risiko in der Handhabung und Lagerung von Batterien. Die Perspektive der Logistik ist hier allerdings etwas konservativer. Basis für eine gelingende Zusammenarbeit muss daher ein gemeinsames Risikobewusstsein und Verständnis sein.« Das neue Whitepaper »Batterie-Logistik« des Innovationslabors (s. auch Seite 6) schafft dafür jetzt die Grundlagen.
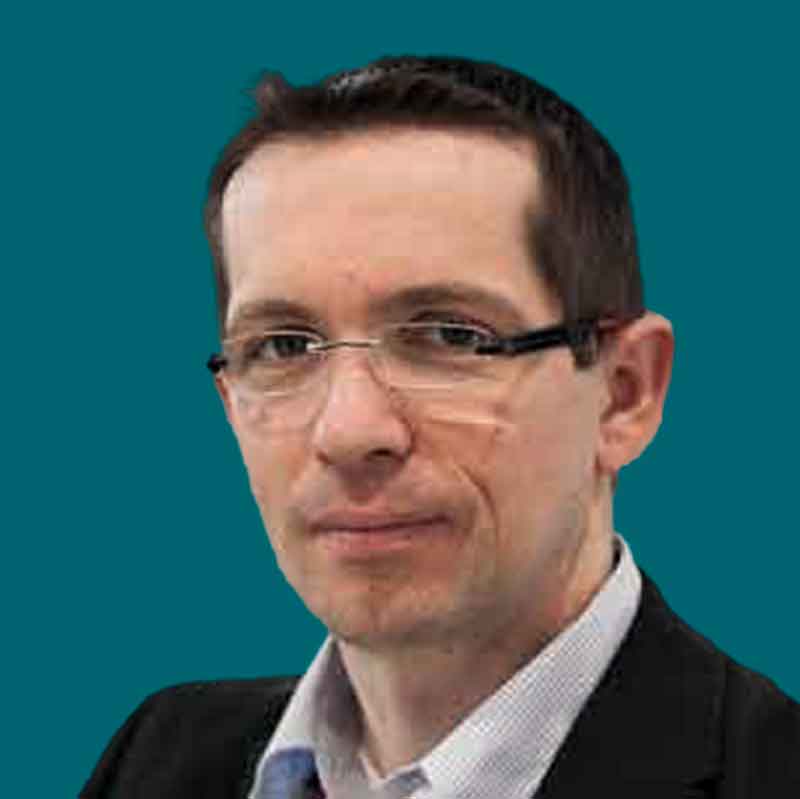
»Für die Batterielogistik von morgen müssen die Perspektiven und Interessen der verschie-denen Akteure in Einklang gebracht werden.«
Dr.-Ing. Arkadius Schier, Projektleiter InnoLogBat
Die Autoren aus Wissenschaft und Wirtschaft stellen den Lebenszyklus von Fahrzeugbatterien aus logistischer Sicht in den Mittelpunkt. Die unterschiedlichen Lebenszyklusphasen implizieren danach jeweils andere Herausforderungen für die Logistik.
Die fünf Phasen im Lebenszyklus einer Batterie
Der Materialfluss einer Lithium-Ionen-Batterie nimmt seinen Ausgang bei den Rohstoff- und Komponentenlieferanten, führt zu den Unternehmen, die Batterien fertigen und sie verbauen, hin zu den möglichen Nachnutzungs- und Verwertungsmöglichkeiten. »Dieser Prozess ist nicht linear, sondern als Netzwerk aus mehreren Lieferanten und Kunden zu verstehen«, so Max Plotnikov. »Das erhöht noch einmal die Komplexität.« Zu den besonderen »Knackpunkten« zählen Lagerung und Transport. Allerdings weist jede Phase im Lebenszyklus einer Batterie aus logistischer Sicht ihre Besonderheiten auf.
Wertvolles Gut
Mit bis zu 50 % der Gesamtkosten ist die Batterie die teuerste Komponente eines Elektrofahrzeuges. Über 70 % der Gesamtkosten einer Batteriezelle werden durch die Materialkosten verursacht.
Quelle: Studie der RWTH Aachen in Zusammenarbeit mit dem VDMA.
Phase 1: Die Beschaffungslogistik umfasst den Einkauf erforderlicher Rohstoffe und Komponenten. Prinzipien der Circular Economy können dabei helfen, eine Unabhängigkeit europäischer Hersteller zu stärken, indem die Verfügbarkeit erforderlicher Rohstoffe durch Wieder- bzw. Weiterverwendung, hochwertiges Recycling und die Rückführung in die (europäische) Wertschöpfungskette sichergestellt wird.
Phase 2: Die Produktionslogistik erstreckt sich von der Materialaufbereitung und Komponentenfertigung bis zur Montage der Batterie und deckt sowohl innerbetriebliche als auch außerbetriebliche Lager- und Transportprozesse ab. Die Produktionsprozesse selbst können aufgrund der hohen Vielfalt der Batterietechnologien, nutzbarer Prozesstechnologien zur Herstellung sowie stets steigender Anforderungen der Batterieperformance variieren.
Phase 3: Der Einbau in das Fahrzeug und der Vertrieb sind Bestandteile der Distributionslogistik. Die Prozesse sind an zahlreiche Vorschriften gebunden. Entscheidend sind neben der Wahl eines geeigneten Ladungsträgers sowie Transport- und Lagersystems vor allem der Zustand der Batterie sowie eine entsprechende Ausstattung und Zertifizierung der Transport- bzw. Lagerlösung.
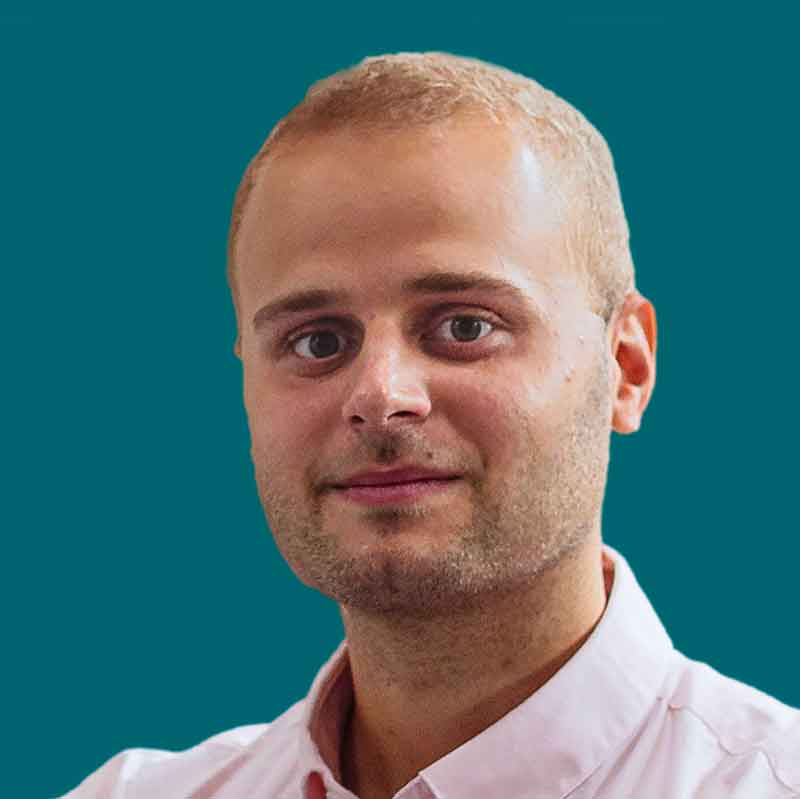
»Entscheidungen zu Sicherheits- und Brandschutzkonzepten von Batterien unterliegen bis heute noch keinem einheitlichen Standard.«
Max Plotnikov, InnoLogBat
Phase 4: Während der Nutzung durch den Endkunden bestehen verschiedene Schnittstellen für die Instandhaltung und Kommunikation zur Batterie. Am einfachsten gestaltet sich die Kommunikation mit einer in ein Fahrzeug eingebauten Batterie, da ein Batteriemanagementsystem (BMS) zur Kontrolle zur Verfügung steht. So hat der Benutzer die Möglichkeit, die Batterie zu beobachten und ihren Zustand einzuschätzen.
Phase 5: Nach der Nutzung, nach etwa acht bis zehn Jahren, haben Batterien in der Regel das End-of-First-Life erreicht und können nicht mehr für die automobile Anwendung genutzt werden. Automobilhersteller sind verpflichtet, diese Batterien wieder zurückzunehmen. Abhängig vom Zustand der Batterie werden die nächsten Schritte im Logistikprozess entschieden. Um die Batterien, verbaute Komponenten sowie verwendete Materialien möglichst lange im Kreislauf zu halten, sind unterschiedliche Nachnutzungs- und Verwertungsmöglichkeiten zu prüfen.
Materialien möglichst lange im Kreislauf halten
Für den wachsenden Elektromobilitätsmarkt müssen für alle beschriebenen Lebenszyklusphasen sichere und vor allem skalierbare Lösungen erforscht, entwickelt und industrialisiert werden. Neben dem Ausbau von Produktions- und Recycling- bzw. Behandlungskapazitäten gehört dazu ebenfalls der Ausbau der logistischen Kapazitäten mit einem einheitlichen Verständnis von Standards für den Transport und die Lagerung von Batterien. Um die Sicherheit aller Beteiligten am Logistikprozess zu garantieren, ist die Qualifikation von Mitarbeitenden im Umgang mit Lithium-Ionen-Batterien unerlässlich. Eine systematische Bewertung der identifizierten Herausforderungen in Form von Risikoanalysen und das Formulieren von Gegenmaßnahmen werden die nächsten Arbeiten des Forschungskonsortiums sein.
Die technoökonomische und ökologische Bewertung von Nachnutzungs- und Verwertungsmöglichkeiten gepaart mit Konzepten für eine regionale Wertschöpfung für den After-Sales-Markt werden weitere Schwerpunkte der Forschung sein, sagt Jan-Philipp Jarmer, wissenschaftlicher Mitarbeiter am Fraunhofer IML und einer der Autoren des Whitepapers: »Ziel ist es, eine Circular Economy von Fahrzeugbatterien weiter zu etablieren und die in den Markt gebrachten Batterien, Komponenten und Rohstoffe möglichst lange im Kreislauf zu halten.«
Sie haben Fragen zum Thema »Lebenszyklus einer Fahrzeugbatterie« im InnoLogBat? Wenden Sie sich gerne an:
Max Plotnikov, wissenschaftlicher Mitarbeiter InnoLogBat, Fraunhofer IML