Die Gesprächspartner
Dominik Gronwald ist Project Manager bei Rhenus Automotive SE in Essen.
Christian Kürpick ist Prokurist / Projektleitung bei der RETRON GmbH, Tochtergesellschaft der REMONDIS Industrie Service) in Lünen.
Sebastian Müller ist Project Manager bei Mercedes-Benz Energy in Kamenz.
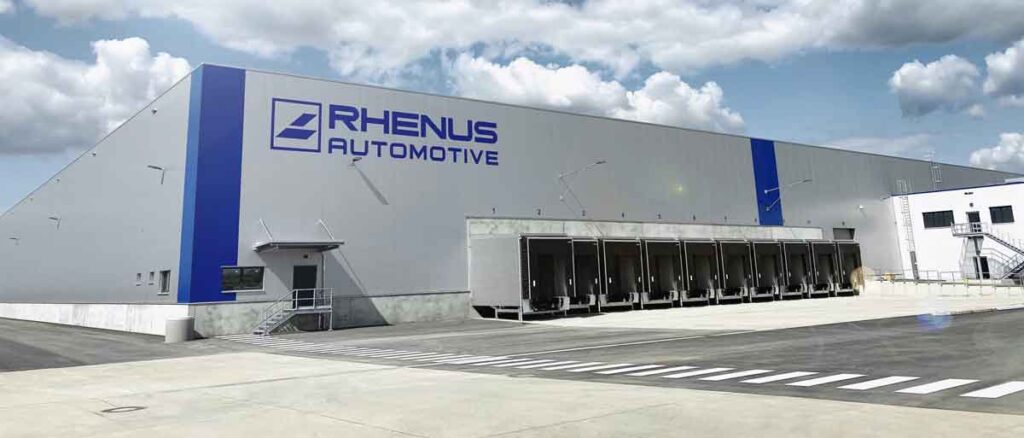
Die Batterielogistik gilt als ein Schlüsselfaktor für den Ausbau der Elektromobilität. Welche Herausforderungen bestehen aus Sicht von Rhenus Automotive?
Dominik Gronwald: Mit dem steigenden Anteil der Elektromobilität bei PKW und Nutzfahrzeugen wandelt sich die Supply Chain für die Fahrzeugherstellung. Daneben steigt die Bedeutung und der Anspruch an Wiederverwertung und Entsorgung von Fahrzeugen und Komponenten. So ist jetzt bereits erkennbar, dass sich die Struktur der Lieferanten für Antriebskomponenten stark verändert hat. Neben bereits sehr gut integrierten Lieferanten aus den Supply Chains für konventionelle Verbrenner gilt es nun, parallel dazu neue bisher nicht integrierte Lieferanten für Elektroantriebe in die Supply Chains mit aufzunehmen. Diese Komplexität resultierend aus der Transformationsphase spiegelt sich auch in den Werken der Hersteller wider.
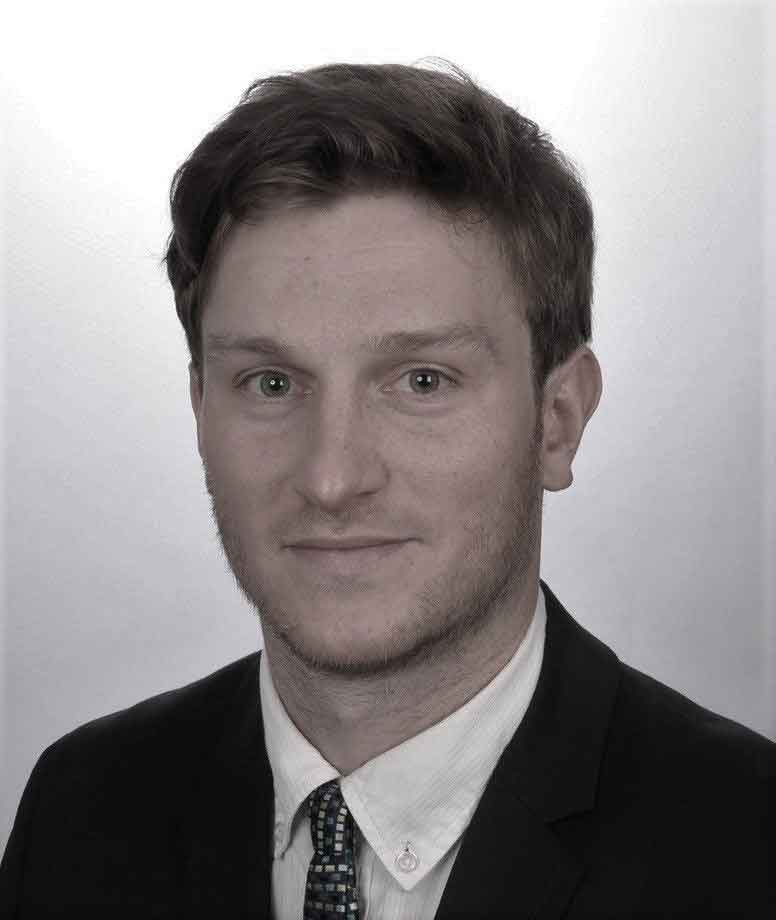
»Die Fahrzeughersteller sehen sich heute einer zunehmenden Ver-antwortung für den gesamten Lebenszyklus der Batterien ausgesetzt.«
Dominik Gronwald, Rhenus Automotive
Wie entwickelt sich die Situation gerade?
Dominik Gronwald: Betrachtet man die Batterien und Batteriekomponenten im engeren Sinne, so eröffnen sich zwei Wege. Zum einen sind das die Anstrengungen der Fahrzeughersteller, selbst leistungsfähige Fabriken für die Herstellung von Batterien aufzubauen. Auf der anderen Seite entstehen neue Komponentenlieferanten, die sich auf der Grundlage ihrer Materialkompetenz für Batterien immer mehr zu Herstellern mit einem breiten Portfolio für Batterie-Systemmodule entwickeln. Es zeigt sich bei der Batterieherstellung, dass auch hier zunehmend Prozesse – angefangen von der Inbound-Logistik, über die Intra-Logistik bis hin zur Outbound-Logistik – von kompetenten Logistik- und Produktions-Dienstleistern übernommen werden. Hier effiziente und nachhaltige Prozesse von der Herstellung bis zur Entsorgung bereitzustellen und mit den OEM effizient und nachhaltig zu betreiben, ist sicher eine der Hauptanforderungen für uns.
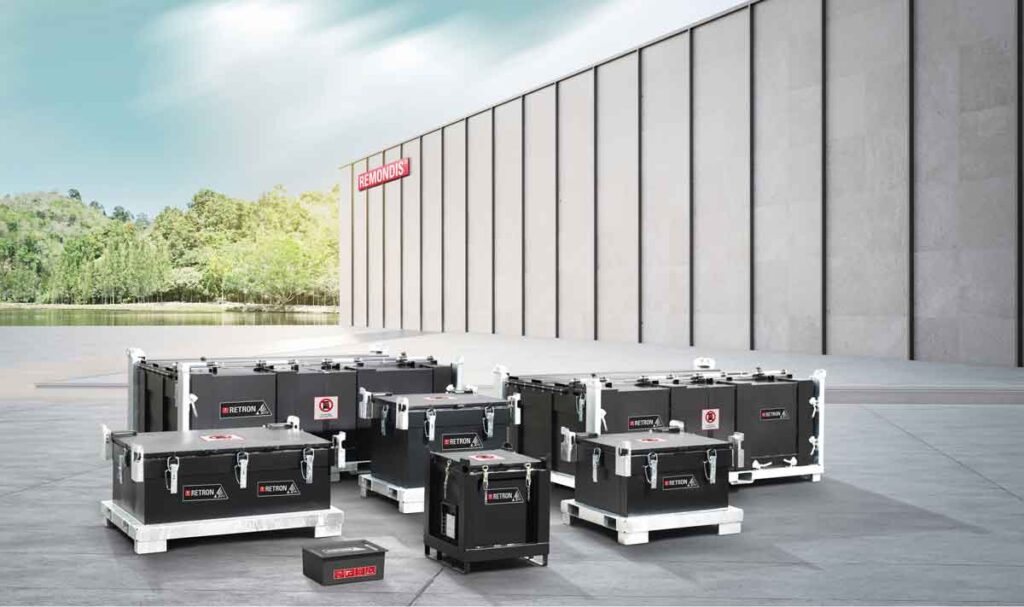
Batterie- oder Automobilhersteller sehen tendenziell eher ein geringes Risiko in der Handhabung und Lagerung von Batterien, weil ihr Fokus darauf liegt, funktionsfähige und sichere Produkte effizient am Markt zu platzieren. Die Haltung der Logistikunternehmen ist da derzeit etwas konservativer. Wie hoch ist das Risikobewusstsein und -verständnis bei REMONDIS?
Christian Kürpick: Lithium-Ionen-Batterien sind in der Zulieferungs- und Entsorgungskette allgegenwärtig. Gerade im beschädigten oder defekten Zustand handelt es sich bei Lithium-Ionen-Batterien um echtes Hochrisikomaterial. Sie können in Brand geraten oder sogar explodieren. Es braucht also dringend ein sicheres System für alle, die mit Lithium-Ionen-Batterien umgehen müssen.
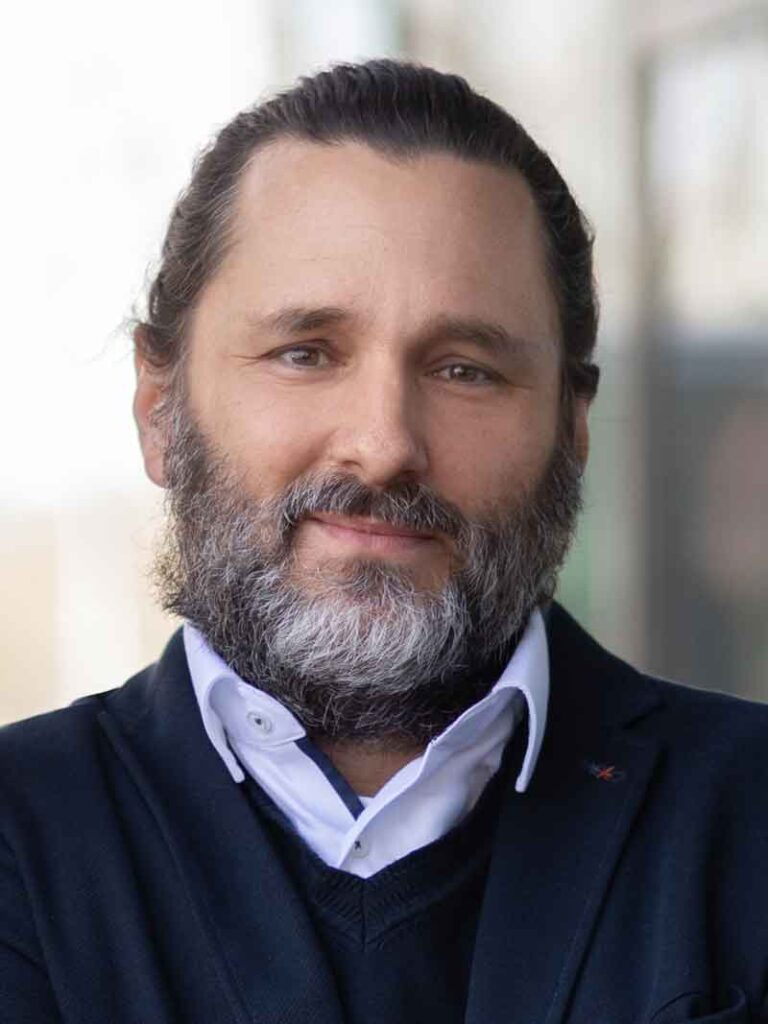
»Mit dem steigenden Anteil der Elektromobilität bei PKW und Nutzfahr-zeugen wandelt sich die Supply Chain für die Fahrzeugherstellung.«
Christian Kürpick, REMONDIS / RETRON
Bei den Sicherheits- und Brandschutzkonzepten zur Lagerung von Batterien gibt es heute noch heterogene Entscheidungen: Je nach Region oder verantwortlicher Behörden reichen beispielsweise mal Rauchmelder an der Ecke, mal wird die Überwachung der Temperatur direkt an der Batterie gefordert. Mal benötigt man nur eine Besprinkelung an der Decke, dann wieder eine Einzelplatzbesprinkelung. Wie gehen Sie bei REMONDIS mit den Themen Sicherheit und Brandschutz um – sowohl bei der Lagerung als auch im Transport von Lithium-Ionen-Batterien?
Christian Kürpick: Mit unserem Behältersystem RETRON haben wir ein sicheres System entwickelt und im Einsatz. Anders als andere Behältersysteme für Lithium-Ionen-Batterien kommt RETRON komplett ohne inertes Schüttmaterial aus. Das Verstauen, Lagern und Transportieren der Batterien ist somit besonders leicht und geht vor allem sauber vonstatten. Zugleich bietet RETRON ein Maximum an Sicherheit. Einmal sicher eingepackt kommen Lithium-Ionen-Batterien dann in UN-zugelassene, hochtemperaturresistente RETRON-Behälter. Sie halten dank hervorragender Isolierung selbst einem eventuellem Thermal Runaway der Batterien mit über 1.000 Grad Hitzeentwicklung mehrere Tage lang stand. Die Außentemperatur der Behälter steigt selbst in einem solchen Fall nicht über 100 Grad.
Was steht bei Ihnen mit Blick auf das Innovationslabor Batterielogistik auf der Agenda?
Christian Kürpick: Gemeinsam mit den Forschenden wollen wir das System noch weiterentwickeln und weiter verfeinern.
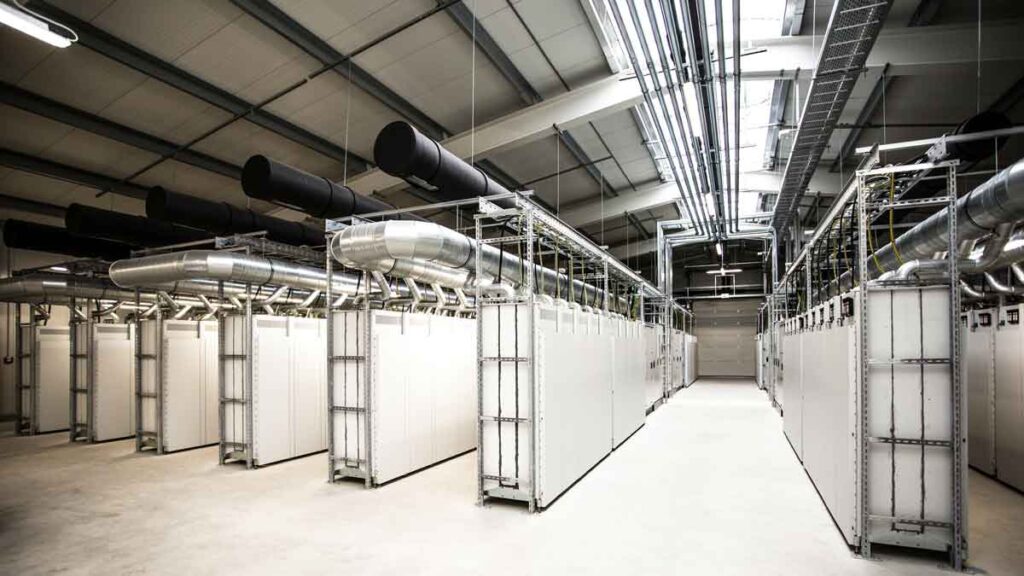
Das Innovationslabor Batterielogistik verfolgt grundsätzlich den Ansatz der Circular Economy. Wie wichtig ist Mercedes-Benz Energy die Nachhaltigkeit der Batterielogistik?
Sebastian Müller: Mercedes-Benz verfolgt mit Blick auf die Kreislaufwirtschaft von Batteriesystemen einen ganzheitlichen Ansatz mit dem Ziel, eine nachhaltige Schließung des Wertstoffkreislaufs von Batterien darzustellen und den Ressourcenverbrauch deutlich zu reduzieren. Das Unternehmen betrachtet dabei drei Kernthemen, wo wir als Mercedes-Benz Energy tätig sind: zirkuläres Design, Werterhaltung und das Schließen des Kreislaufs.
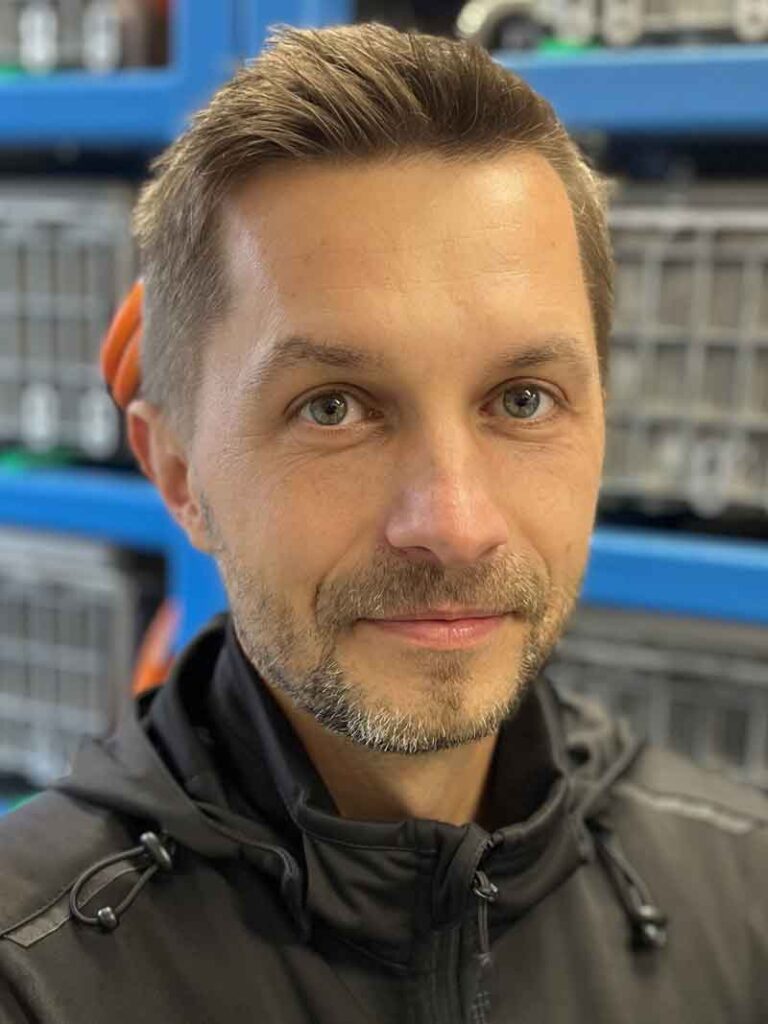
»Mercedes-Benz verfolgt mit Blick auf die Circular Economy einen ganzheitlichen Ansatz mit dem Ziel, eine nachhaltige Schließung des Wertstoffkreislaufs von Batterien darzustellen.«
Sebastian Müller, Mercedes-Benz Energy
Sie haben auch schon frühzeitig entsprechende Projekte durchgeführt …
Sebastian Müller: Wir haben als Tochterunternehmen von Mercedes-Benz bereits 2016 ein erfolgreiches Geschäftsmodell mit stationären Großspeicheranwendungen etabliert. Durch den Aufbau stationärer Energiespeicher bringt das Unternehmen in Zusammenarbeit mit Partnern aus der Energiewirtschaft Elektroautobatterien aus dem Auto ans Netz. Der Fokus liegt insbesondere auf Anwendungen aus dem Bereich 2nd-Life und Ersatzteilspeicher. Der erste 2nd-Life-Batteriespeicher ging im Oktober 2016 im westfälischen Lünen – unter anderem in Kooperation mit REMONDIS – ans Netz. Ein „lebendiges Ersatzteillager“ entstand 2017 am Standort Hannover in Zusammenarbeit mit Partner enercity (Stadtwerke Hannover). Die verlängerte Nutzungsphase maximiert das Potenzial einer Batterie und dabei deren Wirtschaftlichkeit. Gleichzeitig verbessert sie die Umweltbilanz der Batterien, da die wertvollen Rohstoffe im Kreislauf verbleiben. Die sichere Lagerung und Logistik der Batteriesysteme spielen in diesem Zusammenhang eine zentrale Rolle.
Warum engagieren Sie sich im Innovationslabor Batterielogistik?
Sebastian Müller: Die Mercedes-Benz Energy bringt ihre Expertise in das Projekt mit dem Ziel ein, die Technologien branchenübergreifend weiterzuentwickeln.
Wo steht Rhenus Automotive in Sachen die Nachhaltigkeit?
Dominik Gronwald: Die Fahrzeughersteller sehen sich einer zunehmenden Verantwortung für den gesamten Lebenszyklus der Batterien ausgesetzt. Wir sehen daher in unseren Dienstleistungen, in denen wir uns nicht nur um neue, sondern auch die defekten oder älteren Batterien kümmern, die Möglichkeit, die resultierende Komplexität der Hersteller wesentlich zu reduzieren. Diese Aufgabe nehmen wir sehr ernst. Nach der Analyse der gebrauchten oder defekten Batterien entscheiden wir in enger Abstimmung mit den Herstellern, ob sie nach entsprechender Aufbereitung für den primären Anwendungszweck wiederverwendet werden kann oder im Rahmen der Weiterverwendung für andere Anwendungen nutzbar sind. Batterien, die nicht weiter- oder wiederverwendet werden können, werden umweltgerecht und ressourceneffizient entsorgt.
Welche konkreten Möglichkeiten sehen Sie, Batterien weiter zu nutzen?
Dominik Gronwald: Gemeinsam mit unserem Schwesterunternehmen REMONDIS wollen wir ältere Batterien nach entsprechender Prüfung, Bewertung so aufbereiten, dass sie als Batteriespeicher für die Überschussenergie der Solar- bzw. Windkraftanlagen genutzt werden können.
Wie geht es dann weiter?
Dominik Gronwald: Wir achten auch während des Entsorgungsprozesses darauf, dass wir möglichst viele Rohstoffe, aus denen die Batterien hergestellt werden, wiedergewinnen, damit Ressourcen geschont werden können. Das 1st Life einer Fahrzeugbatterie und aller hier relevanten Teilprozesse und Komponenten wird dabei so mit dem 2nd Life und Recycling so vernetzt, dass hierdurch der Kreislauf bestmöglich geschlossen werden kann. Hieraus ergeben sich optimale Gesamtkosten und ein hoher Beitrag für Nachhaltigkeit.
Wir bedanken uns für das Gespräch.
ÜBER REMONDIS INDUSTRIE SERVICE
Als Dienstleister für Industrie, Gewerbe und öffentliche Auftraggeber ist REMONDIS Industrie Service seit mehr als 40 Jahren Experte für die sichere Entsorgung von Gefahrstoffen und gefährlichen Abfällen. Das Familienunternehmen beschäftigt mehr als 3.900 Mitarbeitende an 101 Standorten, verfügt über mehr als 1.100 eigene Spezialfahrzeuge und unterhält 238 Anlagen für gefährliche Abfälle. Pro Jahr werden 2,2 Millionen Tonnen gefährliche Abfälle behandelt und entsorgt.
ÜBER RHENUS AUTOMOTIVE
Rhenus Automotive deckt als Teil von Rhenus Logistics mit seinen 28 Standorten im Bereich Batterielogistik aktuell insbesondere die Themen Inbound-Logistik, Vertriebslogistik, Logistische Zentren (Sequenzierung, Montage, JIT/JIS-Lieferung), Anlagenlogistik, Fahrwerksmodule, Antriebsstrang, Innenausstattung, Module etc. ab. Sehr früh wurde auch die Logistik in Batteriemodulwerken übernommen.
ÜBER MERCEDES-BENZ ENERGY
Mercedes-Benz Energy mit Sitz in Kamenz ist als Tochtergesellschaft der Mercedes-Benz Group AG verantwortlich für die Entwicklung von innovativen Energiespeicherlösungen. Diese basieren auf der automobilen Batterietechnologie, die in Elektro- und Hybridfahrzeugen der Mercedes-Benz Group AG eingesetzt wird. Das Spektrum für die Großspeicher-Anwendungen reicht von Lastspitzenausgleich über Black Start bis zu Unterbrechungsfreier Stromversorgung (USV). Der Fokus des Unternehmens liegt auf Anwendungen aus dem Bereich 2nd-Life- und Ersatzteilspeicher.
Sie haben Fragen zum Thema? Wenden Sie sich gerne an:
Max Plotnikov, wissenschaftlicher Mitarbeiter InnoLogBat, Fraunhofer IML